Warehousing & Logistics
What are warehouse operations?
Warehouse operations is a set of warehouse processes and procedures that ensure the materials flow smoothly in and out of the warehouse. The growing role of large warehouses necessitates a need for well-organized operations, becoming an essential ingredient offering competitive advantages for supply chain companies. Consequently, inefficiencies can erode customer satisfaction and reduce profitability. Warehouse operations management must therefore focus on optimizing processes.
Our operations management, along with planners and other management, uses the clients data to organize the warehouse floor in such a way that the most popular or quick-moving goods are strategically placed.
Our operations group works with clients by investing in warehouse and logistics software systems that support and link all parts of the supply chain.
Our warehouse operations personnel provide the knowledge and expertise to ensure that all inventory is properly received, stored, picked, packed, and ready to be loaded for shipment in the most efficient way possible. We work with our clients to tailor make the complete warehouse and logistics operations fall in line with our customer’s needs.
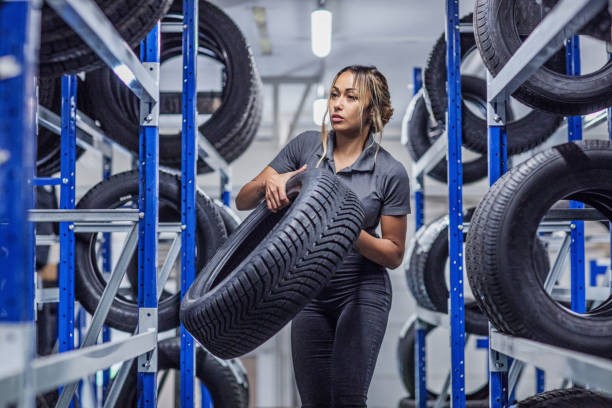
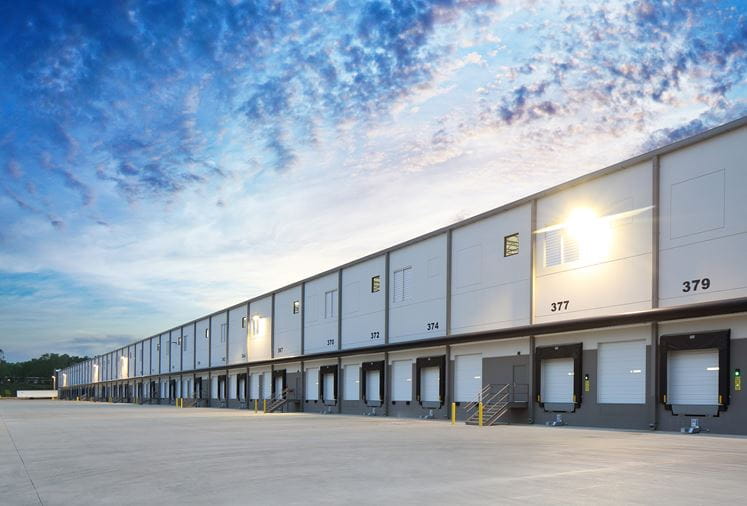
MELIG GRUUP focuses on six main categories for warehouse operations:
- Receiving:
When incoming goods are received, checked, and labeled. - Put-away:
Placing the received goods in the designated storage areas. - Storage:
Tasks related to organizing and operating the warehouse storage area to be space-efficient and process-efficient. - Picking:
Automated or manual picking of orders, B2B or directly to the consumer. - Packing:
Picked items are packed in boxes or safely secured if bulk and made ready for shipment. - Shipping:
Transferring the processed items to the transport company and checking them out.
At MELIS GRUUP we take the security and safety of our employees seriously
Safety – According to OSHA, the fatal injury rate for warehousing is “higher than the national average for all industries.” Because of this fact, agencies, like OSHA, pay extra close attention to common warehouse operations pitfalls, including improper licensing/training procedures, faulty infrastructure, poor recordkeeping, facility maintenance issues, and more. Following the established safety rules ensures that the health of the associates and the business remain secure.
Organization – Our company stresses the importance of storing all materials in standardized bins or marked areas, and in locations that are strategic and well-labeled. We strive to implement operational procedures that reduce cycle time and material handling costs that provide premiere services to our clients.
Communication with the planning team – Too often, organizations experience communication breakdowns between the personnel working on the floor and those working in the corporate office. While a planning team might be aware that factors like globalization could affect inventory cycle times, the warehouse might not learn of this until the 11th hour, when it can only survive, not strategize. This common scenario can be remedied by more frequent meetings and daily communication between the supply chain operator and the client.
MELIS GRUUP stands ready to provide tractors, trailers, drivers, and other supply chain logistical resources that exclusively cater to and are devoted to serving specific clients, facilities, or lanes in a transportation network. We specifically look for clients that require tailored resources as a carrier committed to serving the logistical needs of targeted clients and customers.
The dedicated freight arrangement between specified clients and our logistical assets, where the carrier (MELIS GRUUP) focuses our equipment to haul consistent truckload shipments in the same known lanes and facilities at a fixed rate for a contracted period of time. As we grow we work with the client to find ingenious ways to provide better delivery times, cost savings and a established relationship allowed to evolve and cater to the client.